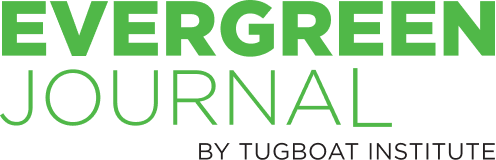
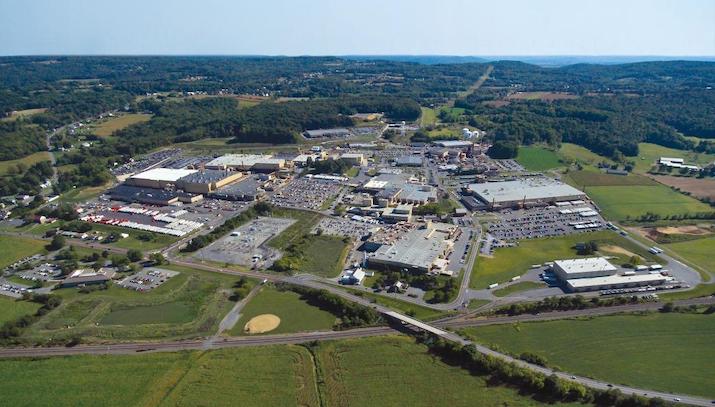
The Most Successful, Yet Little Known, Recycling Program Since the 1950s Has Evergreen Roots
- Chris Pruitt
- East Penn Manufacturing
Sustainability has been the driving force behind our Evergreen® company, East Penn Manufacturing, since DeLight Breidegam, Jr. and his father, DeLight Sr., founded the company in 1946.
When DeLight Jr. returned home to rural Pennsylvania after serving in the Air Force in WWII, he and his father noticed the shortage of materials available to manufacture batteries and began collecting and rebuilding old batteries to meet the post-war demand. For DeLight Jr., who was raised during the depression, recycling in this way was common sense.
That sense of pragmatism and what he would have called “common sense” forged the foundation of many of the practices that DeLight Jr. went on to implement as he grew the company to become a global leader in battery manufacturing. He always had a long-term view, and, for him, that meant building a company that would look after the environment, employees’ well-being, and the community.
I was lucky enough to work with DeLight Jr. when he was still actively leading the company, and he used to say to me, “Pruitt, they’re not making any more land, so we’ve got to take care of it.” That pragmatic expression of environmental stewardship is at the core of East Penn’s steadfast commitment to sustainable practices, and it propels our recycling efforts, which are a pillar of our environmental protection plan.
When people hear about the scale of our recycling programs, they’re often surprised. We manufacture lead batteries—the type in most cars, trucks, and other vehicles today—and many people aren’t aware that 99 percent of lead batteries in the United States are recycled. (In comparison, only 40 percent of aluminum cans are recycled.) This is perhaps the biggest recycling success story that never makes the headlines.
At East Penn, following DeLight Jr.’s early lead, we’ve been recycling since the 1950s, when these practices were not as widespread, to say the least. Why? It comes back, again, to our founder’s common-sense approach to growing a company for the long term. It absolutely makes economic sense to create a sustainable product with a circular life cycle, but it also aligns with our commitment to environmental stewardship because if the batteries were not recycled over and over, they’d be considered hazardous waste.
Instead, we receive spent batteries back at our facility, where we process approximately 30,000 batteries per day, safely recycling all of the components—lead, plastic, and acid—and creating new batteries with about 80 percent recycled materials. We also recycle all of the corrugated cardboard and shrink-wrapping materials we use to package the batteries for distribution via an external recycling entity.
Our investment in the facilities and technology to recycle has been considerable over the years. We built our smelter in 1947 and the battery industry’s first acid reclamation plant in 1992. In 1996, we built a $14 million industrial wastewater treatment zero-discharge facility. We have seven or eight miles of pipe laid underground here at East Penn, and no wastewater leaves our premise. None. It’s all processed, cleaned, and reused. The only water that leaves our premises is the sanitary waste, which goes to the local waste municipality. These long-term, common-sense investments keep the company sustainable and reduce our impact on the environment. We never second-guess those financial commitments.
Looking ahead, we continue to innovate in our environmental stewardship efforts. We use a great deal of energy charging the batteries we produce, so we just embarked on an Energy Efficiency Program to work toward reducing our energy use by more than 10 percent over the next ten years. It’s a collaborative program with the federal government, and it’s one more way we are hoping to improve our impact.
Conclusion
All of the choices we’ve made over the years to limit our impact on the environment and create a truly sustainable product speak to our bigger commitment to building a long-term, sustainable business. But for us, sustainability means more than environmental stewardship. It means reinvestment back into the business. It means proper health and safety procedures to protect our employees. It means providing health insurance for our employees and their families. It means continual innovation. It means taking reasonable risks to grow the business. It means building a strong culture that upholds towards our employees, our customers, and our community.
All of these steps toward sustainability continue to reflect our founder’s common-sense approach. DeLight used to say to me all the time, “Pruitt, it’s not one big thing. It’s a million little things that make a business tick every day, and it’s those million little things that are important because they add up to the big thing of sustainability. That’s our why.”
Chris Pruitt is CEO and President of East Penn Manufacturing
More Articles and Videos
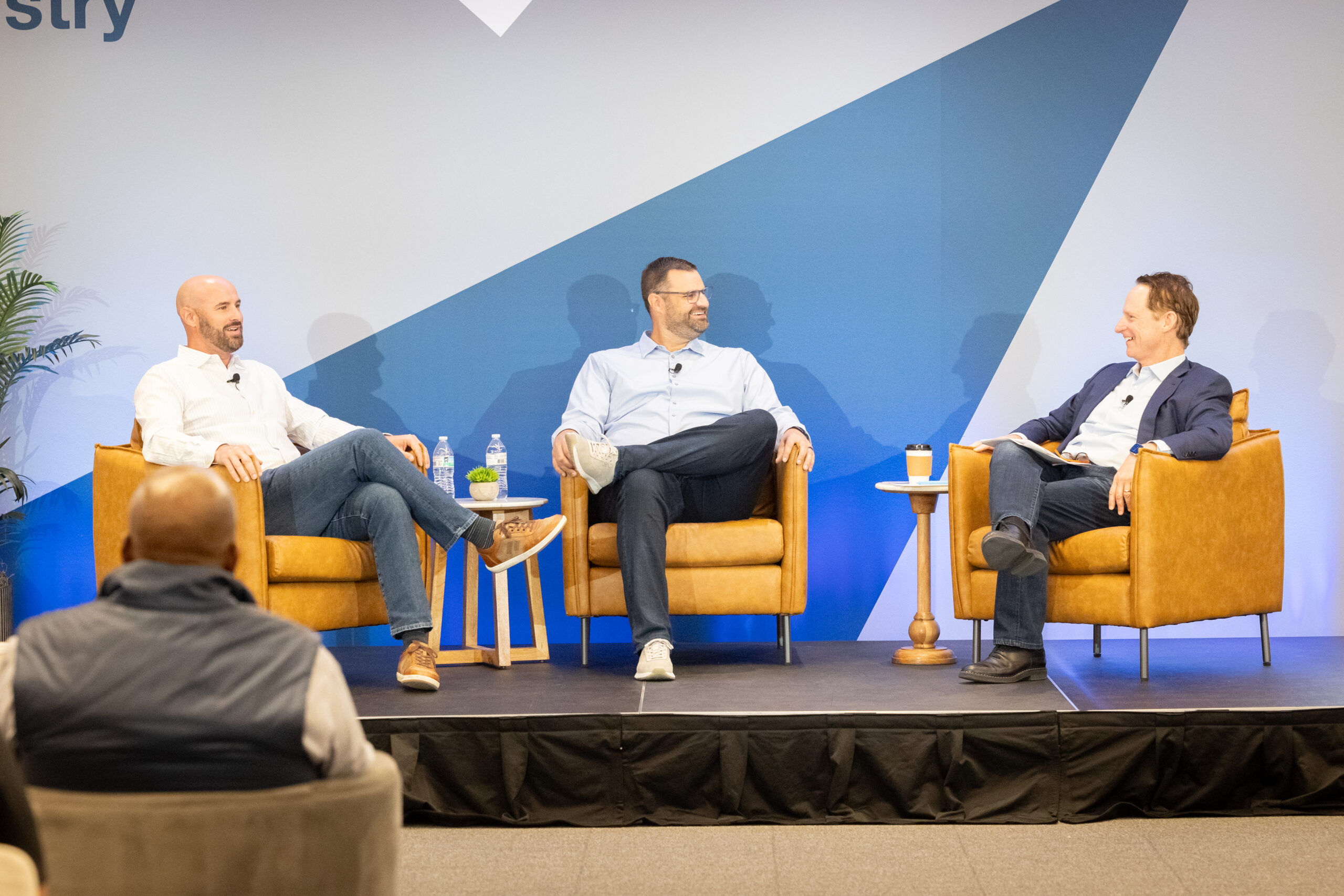
Fireside Chat with Dave Thrasher, Dan Thrasher, and Dave Whorton
- Dave Thrasher, Dan Thrasher, & Dave Whorton
- Supportworks and Thrasher Group
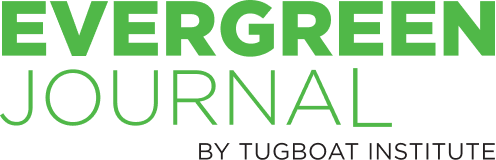
Get Evergreen insight and wisdom delivered to your inbox every week
By signing up, you understand and agree that we will store, process and manage your personal information according to our Privacy Policy