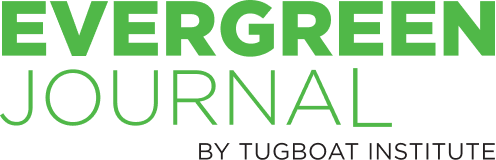
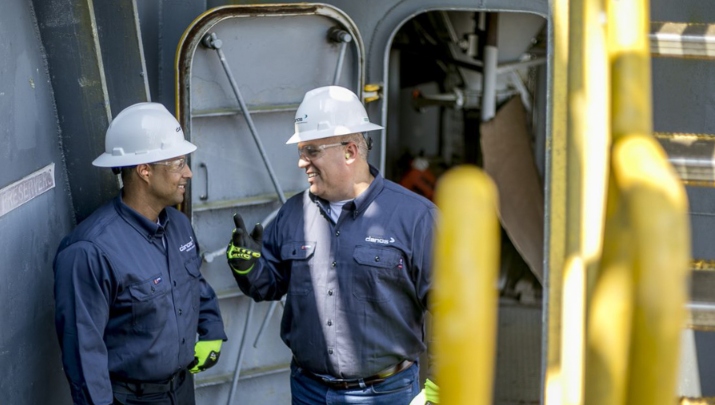
People First Drives Pragmatic Innovation
- Paul Danos
- Danos
When you have employees working on oil production platforms and you are committed to People First, every person in your company must be serious about safety.
People First came naturally to Danos when my grandfather and his brother-in-law started the company in 1947; the initial team was almost all family members. By the time the company got big enough to hire from the outside, the culture of care and connection was firmly set. As an Evergreen® company, People First defines and drives everything we do today. It’s in our DNA.
We are in a high-risk industry: operating and maintaining oil platforms, many of which are over 100 miles offshore. We have 2,500 employees today, working across Texas, the Gulf of Mexico, and other remote parts of the country. We attribute much of our success – on the safety front and elsewhere – to the way we lead from a culture and values standpoint. We do this while tapping into our team’s insights, creativity, and ideas and encouraging experimentation with new technologies to bolster safety through Pragmatic Innovation.
Although our early innovations were not technological, they did have a notable impact on safety. The first one that comes to mind happened in the early 1950s. During that time, crew members boarded boats using ladders attached to a vessel’s exterior, which was very dangerous. So, we designed and built a tugboat with an innovative safety feature – an interior ladder that brought workers from the pilothouse to the galley and the engine room without going outside.
In the early 2000s, we began hosting Safety Focus forums. These intensive, one-day safety events happen throughout the year in key locations where our employees live and work. The day kicks off with a few safety presentations from management to set the tone, but the event mostly focuses on group work, breakout sessions, and time together. The format allows our employees to experience our culture of collaboration through open and honest communication and relationship building. We teach at these forums, but more importantly, we listen. From experience, we know we can learn as much from our employees on the ground about where we can improve on safety as they can learn from us.
One of our first true technological innovations came years ago as an improvement to something that existed already in our industry called Behavioral Based Safety (BBS). We track near misses–incidents where small changes in conditions could have caused injuries. For example, a common interaction with equipment might result in a brush burn, but the incident makes us realize that the potential for serious harm is there, so we enact changes to the way our people interact with that equipment. Although this practice is standard across the industry, it has always been inefficient and slow. So, we decided to start collecting feedback on forms that we could read with a scantron (a technology innovation at that time) to process more information faster.
More recently, with smartphones, we figured out a way to use a simple app to collect and share the data in real-time, which we use today. All near misses are recorded on the app and reported company-wide immediately; notifications pop up on everyone’s phones. We didn’t invent BBS, but as far as I know, we were the first ones to use an app to create instant push notifications. These experiences with the Safety Focus forums and the app reinforced for our leadership team the importance of involving the entire team in Pragmatic Innovation.
In 2015, we decided to try something new by opening an innovation lab in Louisiana. We bought a drone, virtual reality (VR) goggles, and a 3D printer. We invited employees to explore the new tech tools. No one was sure what we were after at first, but eventually, our team came to understand that this lab was about unleashing their creativity. Their ideas started emerging.
As we began understanding the potential for tapping into our team’s creativity, our IT department took the initiative to help us innovate in safety. They developed a whole new platform to capture, organize, and analyze our safety-related data – near misses, serious accidents, and proactive efforts to prevent incidents. As a result, we ended up with a unique, fit-for-purpose platform that has significantly improved accountability, helps identify risks, and generates risk mitigation actions that keep our team even safer.
More recently, we’ve been working on an exciting technology-enabled safety innovation that leverages VR. We built a virtual oil platform – just like the ones we service and maintain — for employee competency testing and training. So instead of having an experienced trainer and new employee meet at a shore-based heliport, fly out to an oil platform in the middle of the ocean, and verify the new employee’s competency on-site, we can do all of this in our virtual oil platform. It’s much safer and has the added benefit of allowing us to test and train every employee on a much wider variety of equipment and different platforms.
We have taken this program even further by creating animation that allows users to “peel back the layers” of the equipment and see inside to better understand the components and how they function. I did this virtual “peeling of equipment” myself, and it helped me understand the processes we manage in ways I never had before. This innovation has made the training experience for new and returning employees much safer. And it all started with placing a few VR goggles in our innovation lab and creativity being unleashed.
If you are committed to being People First, as we are at Danos, safety is a value. We are proud of the success we’ve had on this front. Our OSHA rate, or rate of accidents per 200,000 employee hours, is among the lowest in the industry. We attribute this success to our 75-year history of People First values and strong culture, enabled by our safety programs and Pragmatic Innovation. When you take care of your people and tap into their energy, ideas, and creativity, things can take off in exciting and unexpected directions. For us, it was safety first. We’ll see what’s next.
More Articles and Videos
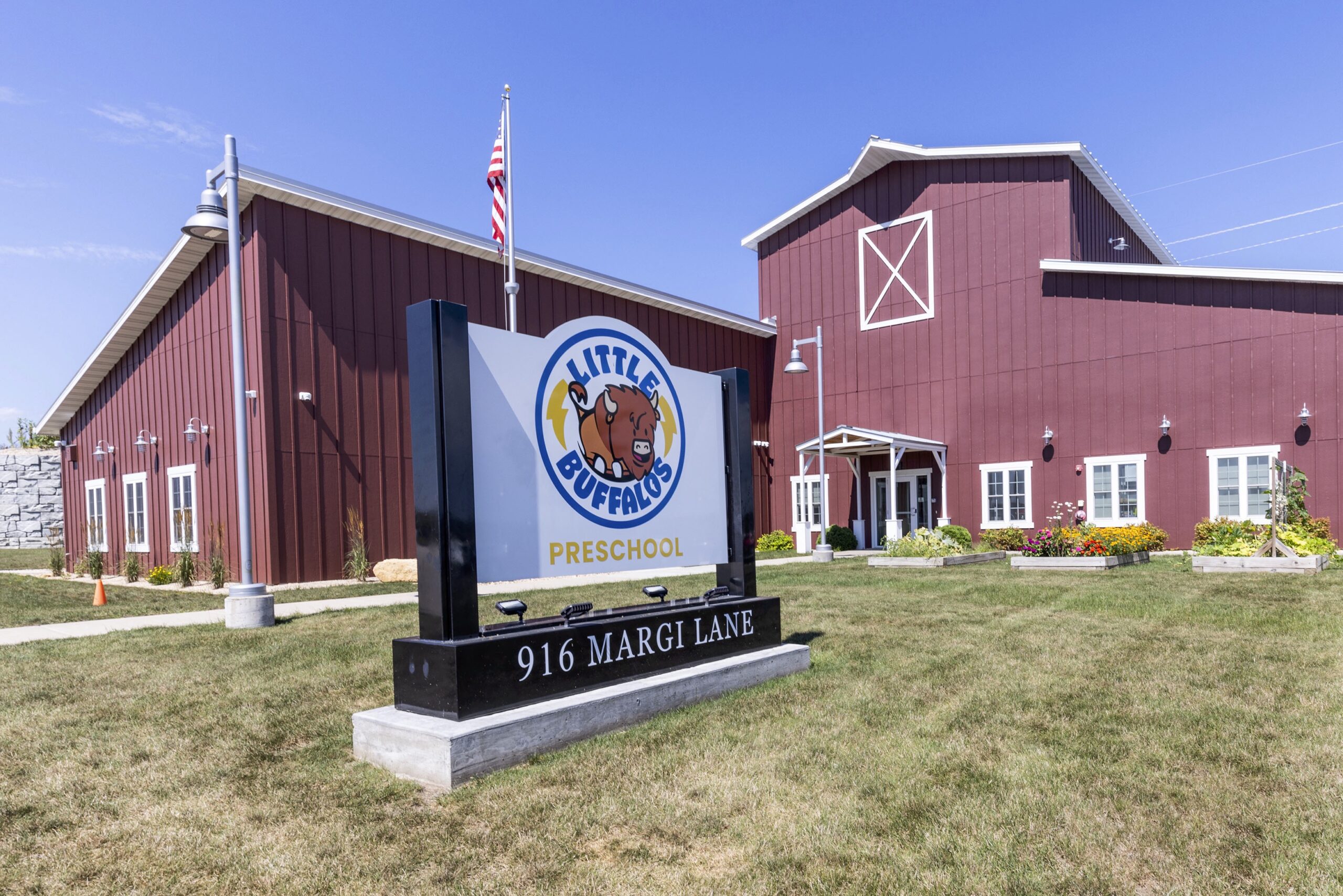
Be the Buffalo: Why an Optics Company Opened a Preschool
- Joe Hamilton
- Vortex Optics
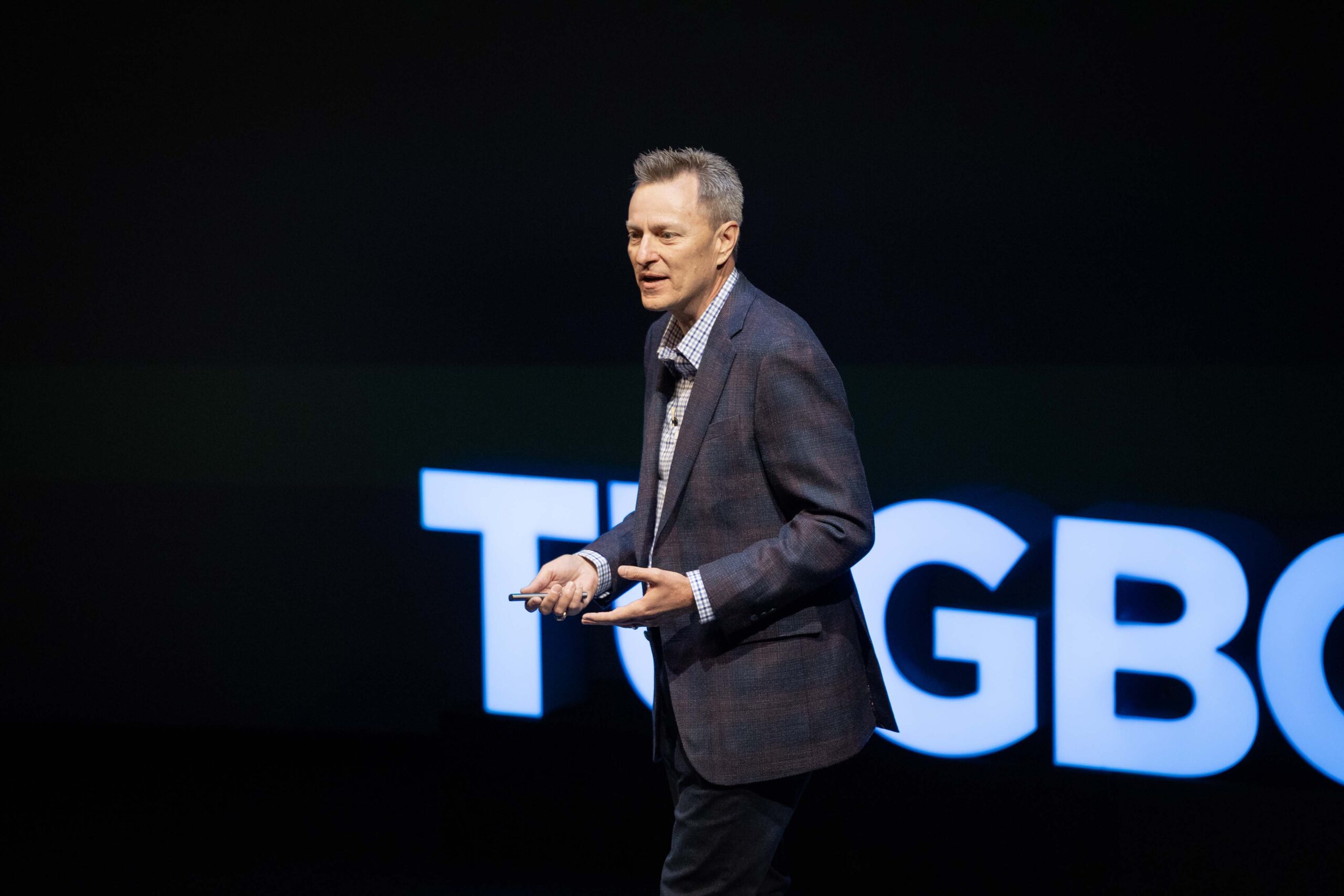
The Making of a 100-Year Company: My Journey to Employee Ownership
- Brad Herrmann
- Text-em-All
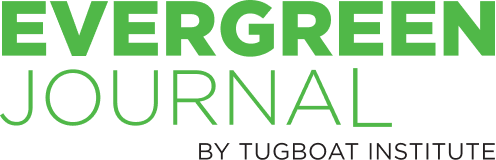
Get Evergreen insight and wisdom delivered to your inbox every week
By signing up, you understand and agree that we will store, process and manage your personal information according to our Privacy Policy